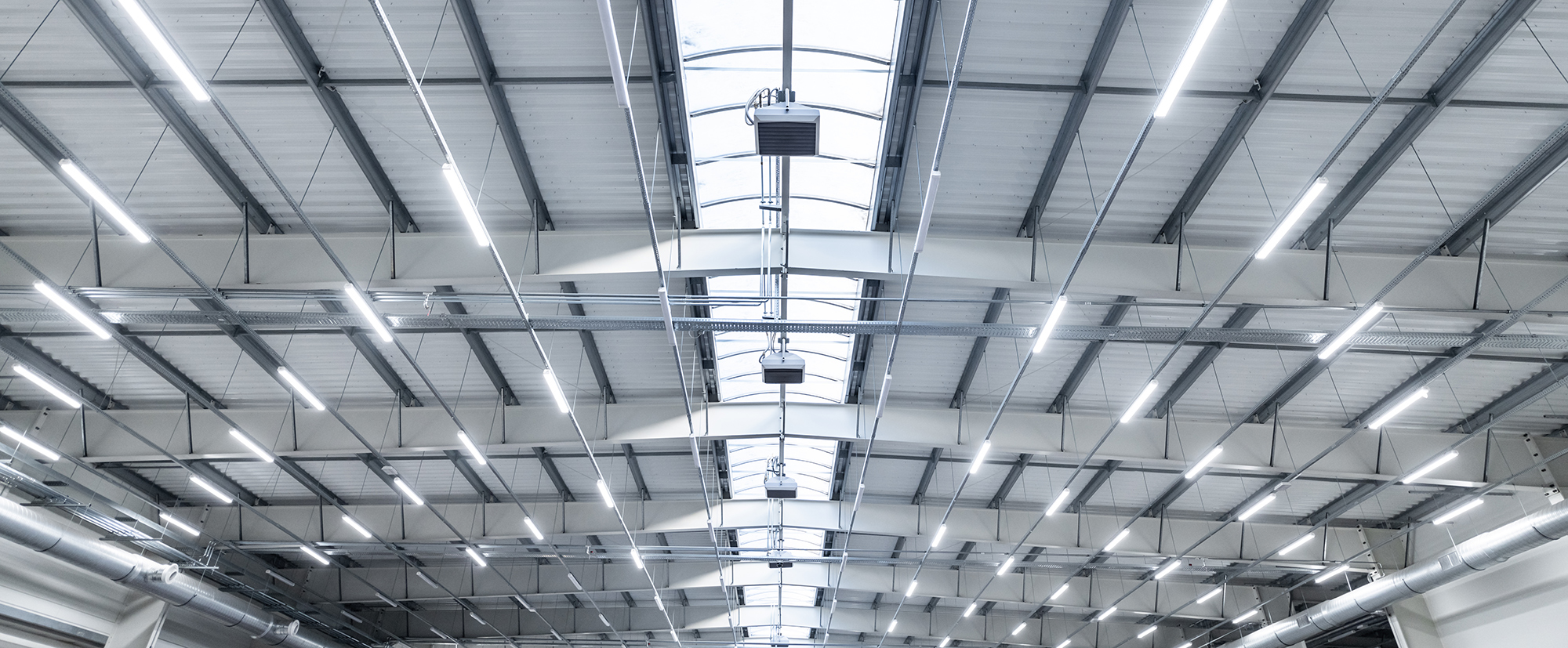
Energy-Saving Tips for Businesses
How you select and manage the use of heating, ventilating and air-conditioning (HVAC) units and lighting systems has a significant impact on your costs. See tips and resources below.
Track your usage
MGE provides your energy use history in My Account. You can view and download your history and use it to track your cost savings from making energy efficiency improvements.
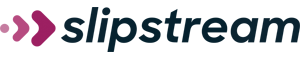
Energy webinars
Slipstream, a trusted expert in energy leadership, has a library of webinars on energy efficiency topics. These live and on-demand videos are free to view. Browse through the Slipstream catalog and see how you can become more energy efficient.
MyMeter
An energy dashboard for MGE business customers to monitor electric and natural gas usage data.
Learn moreEnergy Assessments
Virtual and on-site options to help identify energy-saving opportunities.
Get startedWays to save
The top ways to save energy are often some of the simplest:
- Unplug or turn off lights and other equipment when they aren't being used.
- Set back or lower temperatures for heating equipment and raise temperatures for air-conditioning equipment.
- Review your operations and use timers, sensors and programmable setback thermostats to control lighting and other equipment, especially during on-peak hours. Consider shifting some operations to off-peak hours or scheduling routine equipment tests during off-peak hours.
- Clean and maintain heating, ventilation, air-conditioning and refrigeration equipment regularly. Good maintenance practices can save up to 15% of system energy use and prolong equipment life.
- Invest in new, energy-efficient equipment and technologies to reduce your energy use and increase your productivity, convenience and comfort. Look for ENERGY STAR® ratings for appliances and office equipment. Consider adjustable speed drives to improve motor operations and reduce power demands.